<section>
Пробоподготовка непрозрачных образцов для оптической микроскопии
Непрозрачные образцы - все металлы и большинство материалов из керамики, минералы и полимеры исследуют в режиме отраженного света. При наблюдении исследуется и анализируется только поверхность образца, поэтому подготовка поверхности крайне важна. Под пробоподготовкой, как правило подразумевается:
- получение плоско-параллельной поверхности для достижения фокуса изображения по всей наблюдаемой площади
- удаление загрязнений оставленных при контакте поверхности с предметами, веществами, а также жирами оставленными пальцами рук, нежелательных продуктов, образующихся при взаимодействии поверхности с воздухом (оксидирование). Кроме того, в случае деформационной обработки важно устранение наклепа поверхностных слоев.
- удаление царапин, повреждений и дефектов с поверхности образца, как после технологических процессов производства, обработки. Царапины также вносятся в ходе пробоподготовки от шлифовальной бумаги или диска с более грубым абразивом.
Без пропобоподготовки не только в материаловедении, петрографии, минералогии, но и во всех других областях, медицине, фармакологии, химического и элементного анализа (спектроскопии) и др. очень сложно или почти нереализуемо получить достоверные и воспроизводимые результаты. Использование подобных результатов ведет к неправильной интерпретации и ошибкам в решении задач.
Общепринятым методом является поэтапная пробоподготовка образцов в результате которой образец должен иметь плоскую, качественную, бездефектную (для невооруженного глаза), зеркальную поверхность. Как правило, пробоподготовка подразделяется на следующие этапы:
- Резка – образец отрезается до нужных размеров и формы на отрезных станках с использованием отрезных дисков или при помощи электроэрозионной резки.
- Монтирование образцов в смолу – зачастую хрупкие, а также маленькие и тонкие образцы требуют их монтировки в смолу чтобы избежать разрушения или деформации. В случае маленьких и тонких образцов имеется высокий риск повреждения кожных покровов пальцев, также существует высокий риск того что образец может быть непоправимо завален или вынесен цетробежной силой за бортик и даже потерян в системе для слива воды. Также монтировка крайне важна при наличии трещин в образце, в частности между поверхностью покрытия и образцом, а также при наличии сварочных трещин. Монтирование образцов в смолы важно для хрупких материалов, так как в ходе шлифования, вклад вносимой деформации может быть достаточен для того чтобы привести к его разрушению. Смола обволакивая образец будет препятствовать его разрушению за счет распределения деформации по своему объему. Образец в объеме смолы испытывает всеобъемное сжатие, что также сильно препятствует разрушению.
- Шлифование – первый из двух этапов для получения плоско-параллельной поверхности образцов. Шлифование подразделяется на грубое и тонкое. Данная классификация обуславливается зернистостью используемой шлифовальной бумаги или диска. На этапе шлифования, как правило, поверхность образца приобретает плоско-параллельность, происходит грубое, но быстрое удаление поверхностных несовершенств. От оператора зачастую требуется некоторая сноровка, так как на этом этапе риск заваливания образца (нарушение плоско-параллельности поверхности) велик, что ведет за собой необходимость ее устранения либо на шлифовальной бумаге или диске с той же зернистостью или в крайнем случае с более грубой, что нежелательно, в частности для тонких образов или для образцов с отличной структурой по объему. В процессе шлифования важно использование оптического микроскопа до смены каждого шлифовального диска или бумаги в целях оценки наличия рисок и глубоких царапин оставленных от них.
- Полирование – второй из двух этапов. Процесс полировки служит для получения зеркальной поверхности и устранения наиболее мелких дефектов. Их устранение крайне важно для химического и элементного анализа, а также проведения специальных методик исcледования таких как дифракция обратнорассеянных электронов (Electron backscatter diffraction, EBSD). Полирование всегда осуществляется с использованием алмазных и оксидных суспензий для начального и конечного этапа полирования, соответственно.
- Электролитическая полировка - быстрый и эффективный способ полировки образцов сочетающий в себе комбинацию полировки с одновременным травлением. Электролитическая полировка позволяет проявить микроструктуру, растворяя более "рыхлые" участки структуры, как правило соответствующие границам зерен, а также поверхностные дефекты. Несмотря на большие преимущества электролитической полировки, она требует использования специальных электролитов для каждого материала, их приготовление - смешение в правильных пропорциях, а также наличие специализированного прибора. При выборе неправильного электролита и подбора неподходящего напряжения может произойти чрезвычайно сильное оксидирование образца, в особенности вдоль границ зерен, что крайне неудовлетворительно и неприемлемо, в частности для анализа субструктуры при помощи электронной микроскопии.
- Травление - для проявления структуры образца также важно осуществить травление в специальных растворах кислот, щелочей или солей. В монокристаллах скорость травления, главным образом обуславливается кристаллографической ориентировкой. В поликристаллических материалах, то есть в большинстве случаев, характер травления и ее скорость зависят от выбора раствора. Скорость травления зачастую протекает быстрее вдоль границ зерен формируя канавки травления, так как границы зерен "рыхлые", то есть упорядоченность расположения атомов в них зачастую хаотичная, на них часто сегрегируют примеси поэтому они более химически активны и следовательно доступных связей для взаимодействия с атомами травителя у них больше. Для двухфазных и более сплавов, травитель подбирается с учетом способности формирования металлографической текстуры для отличия их друг от друга.
</section>
<section>
Общая информация
Оптическая микроскопия это неотъемлемая составляющая в современной науке и промышленности, используемая от рутинных исследований и контроле качества до крайне специализированных задач с использованием методик и техник контрастирования, которые позволяют визуально распознать составляющие трудные или вовсе неотличимые при наблюдении в светлом поле.
Среднестатистический человек с нормальным зрением способен различать объекты невооруженным глазом размером до 0.2 мм. Однако зачастую составляющие образца имеют размеры гораздо меньше биологического порога зрительного разрешения. Разрешение – это минимальное расстояние между 2-мя точками, когда они еще зрительно воспринимаются как 2 отдельные составляющие (точки).
Для разрешения объектов меньше разрешающей способности глаза используются оптические микроскопы, использующие для получения изображения видимый свет, в отличии от электронных микроскопов, в которых изображение формируется от электронов. Оптические микроскопы способны достичь разрешения объектов приблизительно до 0.2 мкм или 200 нм, вне зависимости от увеличения. Увеличение и разрешающая способность микроскопа не имеют взаимосвязи. Укрупнение масштаба без увеличения разрешающей способности лишь вызовет размытость изображения.
</section>
<section>
На изображении 1.1 схематически отображена микроструктура из 3-х зерен, блеск от каждого зерна зависит от природы (состава) фаз(ы) и кристаллической ориентировки зерен влияющих на интенсивность отражения света.
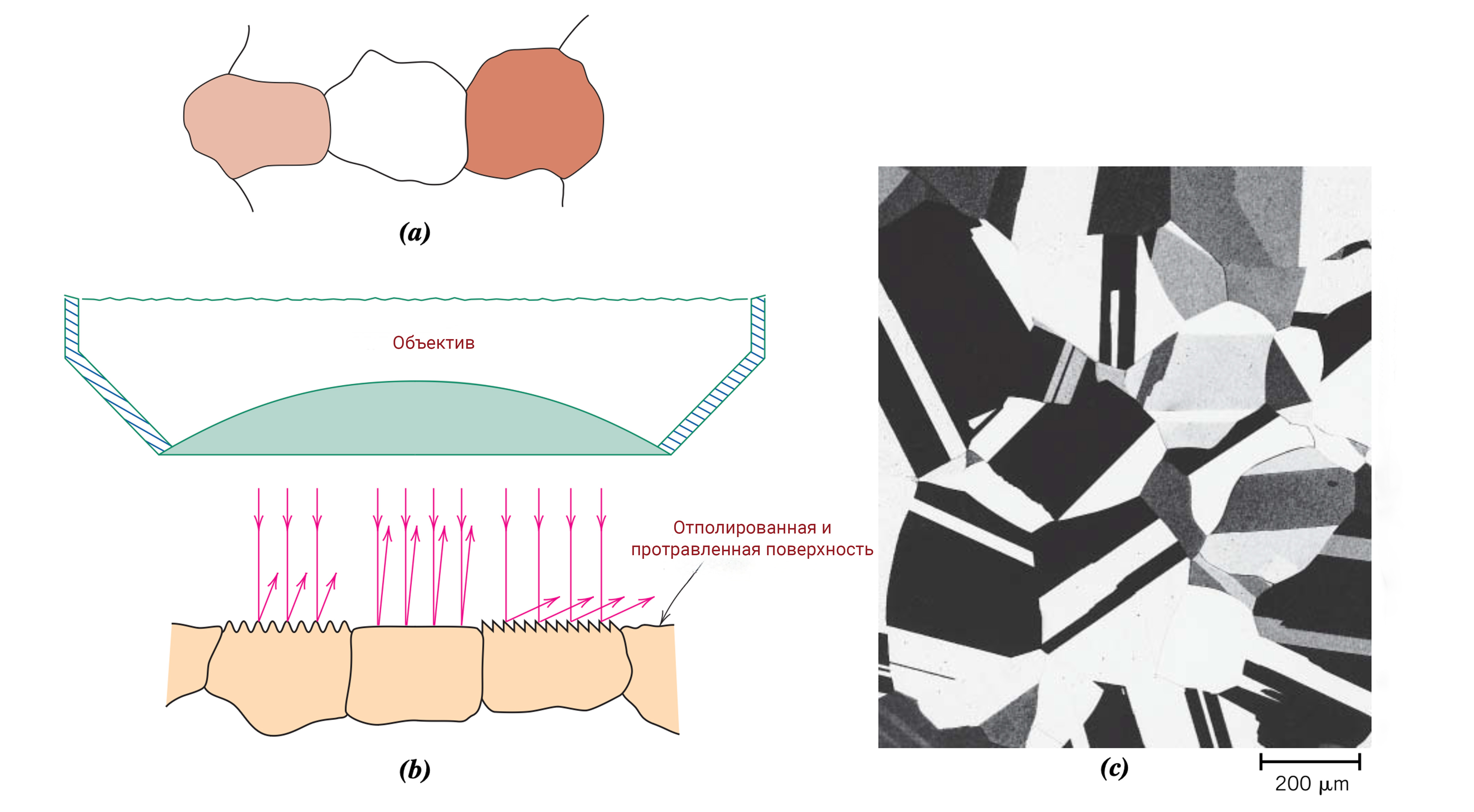
Изображение 1.1 – a) схематическое отображение зерен после полировки и травления в оптическом микроскопе, отличающихся ориентировкой, b) схематическое отображение угла отражения света в зависимости от кристаллографической текстуры и без нее у зерен и с) фотомикрограф поликристаллического образца, с зернами имеющих отличную друг от друга кристаллическую ориентировку (текстуру).
</section>
<section>
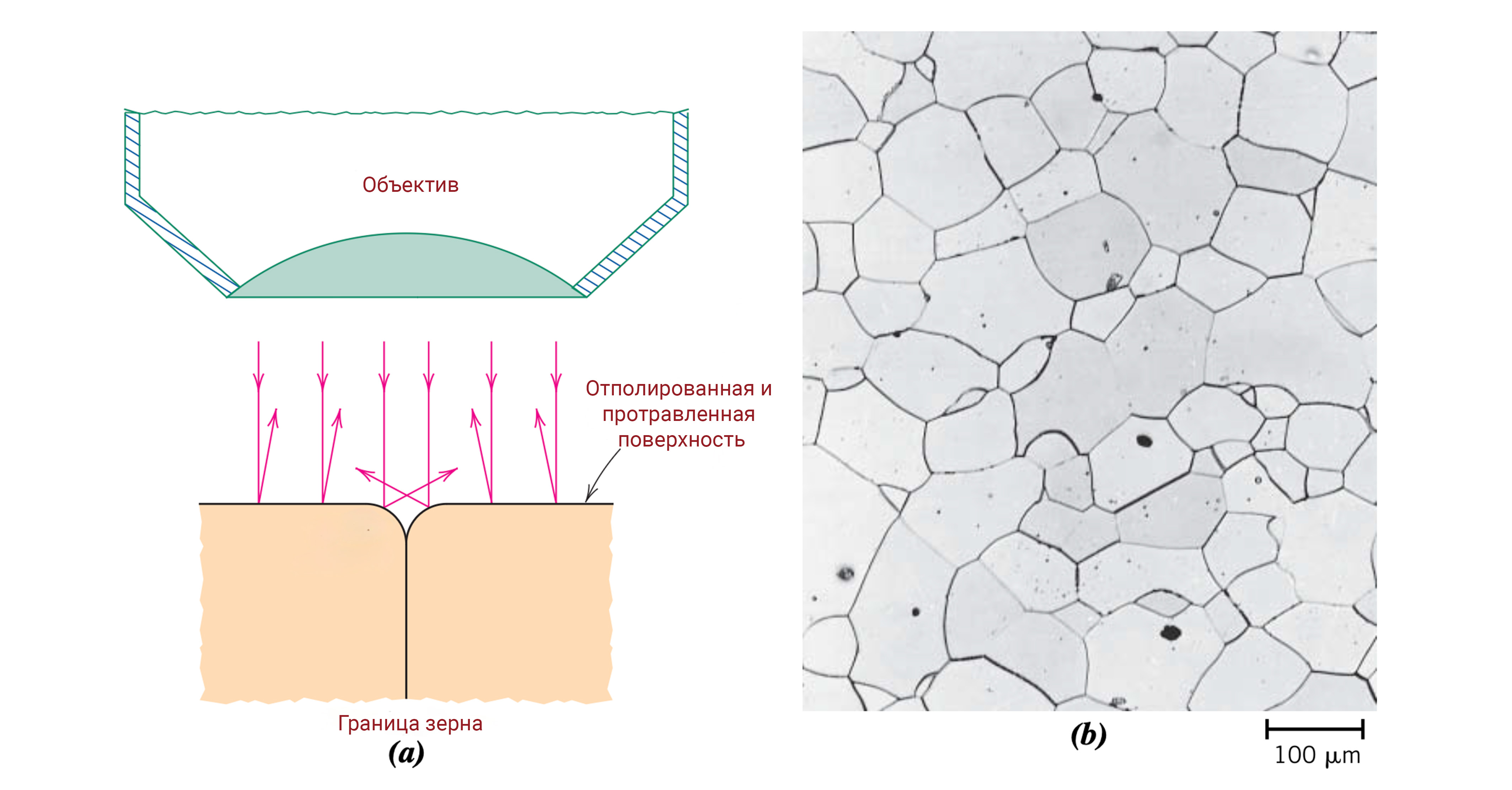
Изображение 1.2 – a) микросктруктура границы зерен с выявленной ямкой травления, b) фотомикрограф отполированной и протравленной поверхности хромистой стали, черные линии относятся к границам зерен.
</section>
<section>
Резка материала
Резка материала необходима для получения образцов нужных размеров и форм. Процесс резки зачастую считается очень важным и требует высокой степени контроля так как на этой стадии приходится наибольший вклад внесения деформации и риск повреждения образца. Большая доля деформации, как правило вносится в область контакта и минимизируется оптимальным подбором режима резки и твердостью отрезного диска и устраняется при последующих этапах пробоподготовки.
Для металлографических исследований и в целом подготовки материала к анализу нельзя использовать отрезные диски изготавливаемые для промышленных целей, так как они вносят большую степень деформации и увеличивают риск повреждения и разрушения материала.
Резка осуществляется при помощи отрезных станков.
Для качественной, бездефектной резки нужно контролировать скорость вращения и подачи либо диска к материалу или стола с монтированным на нем материалом, в зависимости от метода резки. Также крайне важным является выбор отрезного диска из подходящего по твердости материала. Слишком мягкий по твердости диск не будет иметь достаточную режущую способность, он имеет быструю склонность к износу, может привести к повреждению образца или в худшем случае самого отрезного станка. Слишком твердый отрезной диск для мягких металлов может быть достаточно долговечным, но приводит к увеличению стоимости и порой нецелесообразности его использования.
Отрезные станки подразделяются на прецизионные и стандартные.
Прецизионные станки следует использовать для хрупких материалов, так как риск повреждения от прецизионных станков минимален, а также для резки с высокой точностью и резки материалов небольших размеров. Кроме того, прецизионная резка минимизирует отходы материала (неизбежную потерю материала) за счет меньшего размера и толщины отрезного диска.
Прецизионная резка подходит для:
- Хрупких материалов
- Высокоточной резке
- Керамики
- Карбидов
- Нитридов
- Печатных плат
- Биоматериалов
- Стекол
Стандартные отрезные станки следует использовать для крупных образцов. Они чаще всего используются для резки металлов, сплавов и не только. Подобные отрезные станки как правило имеют множество режимов резки, которые зачастую автоматизированны.
Отрезные станки подходят для резки:
- Металлов
- Сплавов
- Больших образцов
- Автоматической резки
- Серийной резки
- Резки некоторых керамических материалов
</section>
<section>
Монтировка образцов в смолы
Монтировка образцов посредством холодной заливки и горячей запрессовки необходима для:
- Автоматических шлифовально-полировальных станков с имеющимся и подключенным к ним компрессором
- Автоматизированных станков с целью установки нескольких образцов в специальные держатели
- Пробоподготовки хрупких образцов для избежания их разрушения
- Небольших образцов
- Тонких образцов
- Идентификации образцов с отличной историей обработки и/или структурой
- Измерения микротвердости
- Снижению износа полировальной ткани
- Удобства пробоподготовки
- Сохранения микроструктуры перед исследованиями
- Хранения образцов
Горячая запрессовка осуществляется при помощи специальной установки с прессом и весьма удобна для быстрой монтировки образцов с высоким удержанием края и подготовки образцов для автоматических шлифовально-полировальных станков. Монтирование образцов при помощи горячей запрессовки стоит выбирать в случае отсутствия восприимчивости образцов к термическому воздействию и давлению.
Холодная заливка является альтернативой без использования пресса и подвержения образца температурному воздействию. Обычно различают акриловую смолу, которая является бюджетным решением и имеет высокую скорость затвердевания и эпоксидную. Эпоксидная смола имеет высокую степень удержания края, но со временем деградирует, крошиться и образует полости.
</section>
<section>
Шлифование образцов
Шлифование, как правило осуществляется на шлифовально-полировальных станках с использованием либо шлифовальных бумаг или дисков для получения плоско-параллельной поверхности образца. Шлифовальные бумаги и диски отличаются зернистостью, то есть насколько грубый по размеру абразив нанесен на их поверхность. Зернистость диска выбирается в зависимости от твердости материала - чем больше твердость, степень наклепа или лишняя выпуклость на поверхности, тем грубее подбирается зернистость.
</section>
<section>
Полировка образцов
Полировка образца осуществляется также на шлифовально-полировальных станках для удаления последних дефектов на поверхности образца (рисок от шлифовальных дисков или бумаг), а также получения зеркальной поверхности. Для полировки используются алмазные двухкомпонентные суспензии, а для финальной ее части, как правильно оксидные суспензии, которые также обеспечивают некоторую степень травления. Кроме того, крайне важным является полировальная ткань, выбор которой обусловлен природой и размером материала, а также типом суспензии - алмазная или оксидная, а также их зернистостью. Для быстроты пробоподготовки и средств, что целесообразно для рутинных исследования в оптическом и электронном микроскопах, также существуют универсальные полировальные ткани. В результате, после полировки получается бездефектная (для невооруженного глаза), зеркальная поверхность.
</section>
<section>
Электролитическая полировка и травление образцов
Электролитическая полировка обеспечивает быструю и эффективную полировку с травлением поверхности образца. Как правило, она требует использование специализированного прибора и электролита, выбор которого обуславливается природой материала, количеством составляющих его фаз. Электролитическую полировку важно осуществлять с правильно выбранным напряжением. Получаемая поверхность, как правило получается зеркальной, бездефектной (для невооруженного глаза или для оптического микроскопа) - границы зерен протравливаются, а оставшиеся дефекты быстро удаляются с поверхности.
Травление дает возможность выявить границы и соответственно формы зерен для анализа при помощи оптического или электронного микроскопа.
</section>